El presente trabajo se propone realizar un estado de la cuestión de la Manufactura Aditiva de materiales cerámicos por procesos de extrusión de pastas basadas en arcillas, repasando las definiciones y la clasificación según los estándares internacionales actuales.
Se describe la categoría de Material Extrusion en sus aspectos generales y se propone la clase Paste Deposition Modeling para la extrusión de pastas que, ya depositadas, solidifican por evaporación del solvente; para distinguirlo, así, de Fused Deposition Modeling, empleado en polímeros extruidos mediante su plastificación por temperatura y solidificados por enfriamiento.
A partir del relevamiento de los antecedentes de la tecnología de impresión 3D por extrusión de pasta cerámica, se propone una clasificación y una historización de las innovaciones en el desarrollo de esta tecnología.
Introducción
Luego de una fase inicial de desarrollo como tecnología de punta durante las últimas décadas del siglo XX, las tecnologías de impresión 3D (I3D) mostraron una enorme expansión en los inicios del nuevo siglo al producirse la difusión de la innovación (Fressoli & Smith, 2015) (Wohlers & Gornet, 2016) (Huang et al., 2015). Este proceso se ha caracterizado por: alto nivel de avances en el ámbito científico-tecnológico; incorporación de las herramientas digitales en el ciclo de diseño y producción industrial; creciente interés del mercado que lo ha llevado a convertirse en un sector de la industria con peso económico propio; la consolidación de las redes comunitarias y globales de uso, aplicación, desarrollo y experimentación, surgidas bajo el modelo de innovación abierta en el contexto de la globalización digital; la popularización en la cultura, como materialización de las representaciones de los futuros imaginarios de la ciencia ficción, con su controversia entre la renovada promesa del progreso tecnológico y la preocupación social por las tensiones que generan las tecnologías disruptivas; y las oportunidades que ofrece para el desarrollo local y su inclusión en la lista de los desafíos científicos y tecnológicos prioritarios en las políticas públicas de innovación y educación.
Mientras se consolidaba como tecnología emergente, la tecnología de I3D fue definiéndose por su propiedad de manipular la materia en forma digital, por «pasar del bit al átomo y viceversa», entendida, además, como la continuación de la digitalización desde el campo de la información y la comunicación al de la producción de objetos (Gershenfeld, 2012).
En el presente artículo nos proponemos realizar una revisión de la I3D por extrusión de materiales cerámicos basados en arcilla, a fin de clarificar las definiciones y describir las particularidades de esta nueva tecnología. Para ello realizaremos un relevamiento de las experiencias recientes en laboratorios, en las comunidades virtuales y en el sector privado, abordando la literatura académica, la información compartida en las redes de conocimiento abierto y la documentación técnica y comercial de las empresas. Luego seleccionaremos los casos más representativos y realizaremos un análisis comparativo que permita elaborar una cronología demostrativa de la evolución del desarrollo tecnológico y proponer una clasificación ordenada de los antecedentes relevados. Finalmente se delinearán los principales desafíos de investigación y desarrollo para la consolidación de este incipiente sector innovador.
1. DEFINICIÓN Y CLASIFICACIÓN DE LA MANUFACTURA ADITIVA
En su breve historia se han utilizado diversas conceptualizaciones del fenómeno de la I3D con sus propias terminologías, a menudo ambiguas y confusas. Algunos de los términos empleados fueron: additive fabrication, additive processes, additive techniques, additive layer manufacturing, layer manufacturing, solid freeform fabrication, freeform fabrication, entre otros.
En el año 2015 la norma ISO/ASTM 52900 establece un marco claro para la Manufactura Aditiva (MA), definiéndola como el «proceso de adición de material para producir una pieza a partir de información digital de un modelo 3D, usualmente capa a capa, en oposición a las metodologías de fabricación sustractivas y conformativas»; y a la I3D como la «fabricación de objetos mediante la deposición de un material usando un cabezal de impresión, boquilla, u otra tecnología de impresión» (ISO/ASTM, 2015). El proceso de fabricación de un objeto desde información digital, como se muestra en la figura 1, se lleva a cabo en diferentes pasos dentro de un sistema, en cuyo núcleo se encuentra la máquina impresora propiamente dicha, donde se realiza el ciclo constructivo basado en la adición sucesiva de material en forma de capas, lo cual distingue a la MA de las metodologías sustractivas y conformativas. Las acciones previas son aquellas realizadas sobre el modelo digital en un software que permite seccionar el sólido en planos sucesivos y calcular las trayectorias necesarias a partir de la carga de los parámetros por parte del operador. Posteriormente a la I3D se realizan operaciones que pueden involucrar la modificación de las propiedades del material o la terminación de la geometría de la pieza.
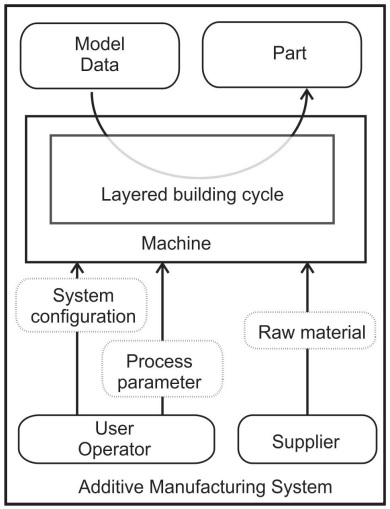
La manera particular en que las diversas técnicas aditivas resuelven el ciclo constructivo aditivo es lo característico de cada una, por ello el criterio principal mediante el cual categorizarlas es el partido tecnológico empleado, considerando los siguientes criterios (Travitzky et al., 2014):
– Según el tipo de elemento geométrico usado como módulo: punto, línea y plano.
– Caracterizando al material no tanto por su composición sino por su estado y su presentación como insumo del proceso: líquido, en suspensión, en polvo, en lámina, en pasta, en filamento.
– En función del método usado para unirlo: sinterización/fusión, polimerización, laminación, extrusión y deposición por inyección.
La ISO/ASTM 52900:2015 establece una clasificación general, organizando el extenso universo de la MA en siete categorías:
– Binder jetting: deposición selectiva de un agente ligante líquido para unir material en polvo.
– Directed energy deposition: unión de materiales que funden por energía térmica focalizada (por ejemplo láser, haz de electrones o arco plasma) a medida que son depositados.
– Material extrusion: dosificación selectiva de un material a través de una boquilla u orificio.
– Material jetting: deposición selectiva de gotas de material (por ejemplo, fotopolímeros o ceras) para la construcción de la pieza.
– Powder bed fusion: fusión selectiva de regiones de un lecho de polvo mediante energía térmica.
– Sheet lamination: adhesión de láminas de material para construcción de la pieza.
– Vat photopolymerization: curado selectivo de un fotopolímero líquido en una cuba mediante polimerización activada por luz.
Dentro de cada categoría, tal como se muestra en la tabla 1, se despliega un segundo nivel de clasificación que responde a las denominaciones que los fabricantes dieron al principio de funcionamiento particular de sus equipos.
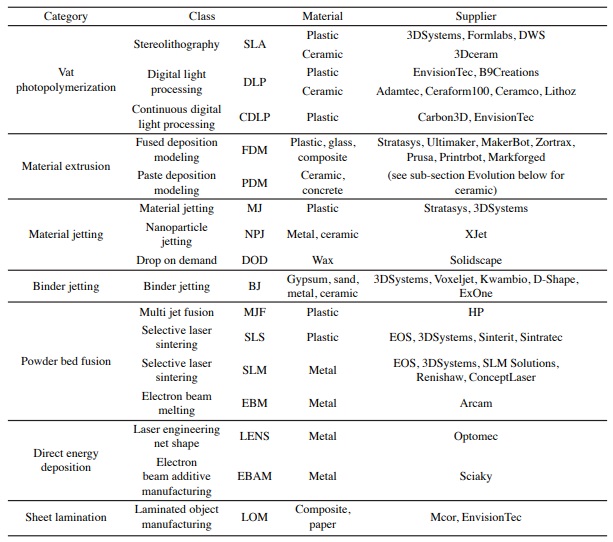
Los materiales cerámicos son empleados en varias de las categorías de MA. En otras reseñas puede observarse que aquellas técnicas que parten de materiales en polvo y en suspensión son las que logran mejores resultados en aspectos dimensionales y en el aprovechamiento de materiales avanzados en aplicaciones de alto valor agregado (Travitzky et al., 2014) (Deckers et al., 2014) (Chen et al., 2019).
Dentro de la categoría Material Extrusion (ME), si bien existen investigaciones en materiales cerámicos no arcillosos, las técnicas basadas en extrusión de pasta de materiales tradicionales son las de mayor difusión en el diseño, el arte y la industria, debido a su bajo costo y al impulso del movimiento de innovación abierta. Por ser resultado de la creación en redes sociales más que de la investigación y desarrollo académico, se presenta como un área de vacancia a analizar a fin de proponer un criterio de clasificación organizado y congruente.
2. IMPRESIÓN 3D POR EXTRUSIÓN DE PASTA CERÁMICA
La técnica fundamental de la categoría Material Extrusion es la conocida como Fused Deposition Modeling (FDM) que se ha convertido en la más extendida en la industria y en el uso profesional y amateur. Empleada exclusivamente en plásticos y materiales compuestos de matriz polimérica, se define como la técnica en la que se extruye un filamento fundiéndolo por calor y forzándolo a pasar por una boquilla, el cual una vez depositado se solidifica al enfriarse.
En el presente trabajo emplearemos el término Paste Deposition Modeling (PDM) para referirnos a un gran número de experiencias que usan pastas, en estado plástico, para las cuales no existe una terminología clara. El proceso es similar al FDM de polímeros salvo que la pasta es extruida y depositada a temperatura ambiente, solidificándose por evaporación de agua u otro solvente (Fig.2). En su reseña de 2014 Travitzky et al. (2015)encuentran una gran y variada forma de denominaciones: Extrusion Freeform Fabrication (EFF), Aqueous Based Extrusion Fabrication (ABEF), Filament Based Writing (FBW), Freeze Extrusion Fabrication (FEF), Direct Ink Writing (DIW), Slurry Deposition, Dispense Plotting, Bioplotting, Rapid Prototyping Robotic Dispensing (RPRD), Microextrusion Freeforming (MF), Multiphase Jet Solidification (MJS), 3D Fiber Deposition (3DFD), y Robocasting (RC).
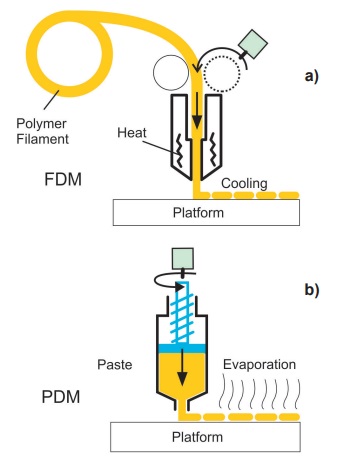
La tecnología de PDM aplicada en la fabricación de cerámicos reemplaza las técnicas habituales de conformado de la pieza en estado «verde», siendo la preparación del insumo y las operaciones posteriores las mismas del método tradicional de fabricación (Fig.3). Como sucede en general con la digitalización de los procesos de fabricación, las principales ventajas son la eliminación de la inversión y los plazos de construcción de modelos, moldes y matrices, la ampliación de las posibilidades morfológicas, y la rapidez y bajo costo de producción de piezas únicas o en series pequeñas.
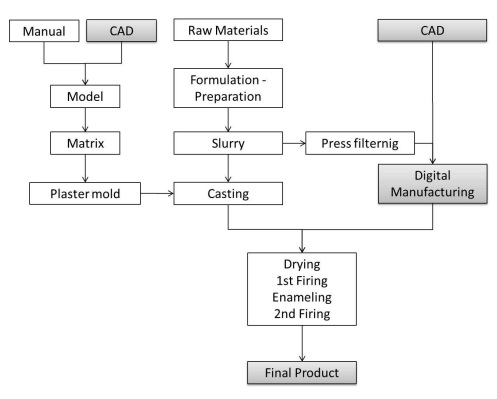
2.1 Principio de funcionamiento de la impresión 3D por Material Extrsusion
La I3D por ME consiste en la deposición selectiva de cordones de material en estado plástico extruido a través de un orificio, sobre una plataforma —que soporta la primera capa— que se desplaza con respecto a la boquilla en forma automática en el espacio —prismático en las máquinas cartesianas, cilíndrico en las del tipo Delta— en un sistema de coordenadas XYZ. El material es extruido por el orificio de la boquilla con una sección circular y al depositarse pasa a una sección de configuración oblonga —que puede ser sintetizada como un rectángulo terminado en dos semicircunferencias a los fines del cálculo de su área (Slic3r, s. f.)— deformándose contra la plataforma o la capa inferior (Fig. 4). La altura del material depositado está fijada para cada capa por la separación en Z y el sólido formado por la traslación de la sección de deposición es generado por la trayectoria de la boquilla gracias a la interpolación de los ejes X e Y.
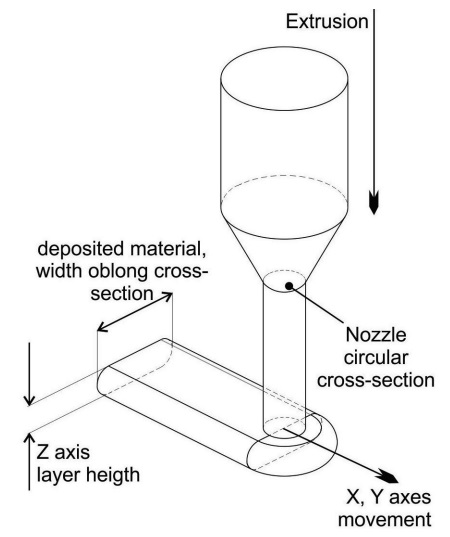
El ancho de la sección depositada se encuentra sin lugar a duda en relación de la relación de velocidades de extrusión y de avance en XY. El control de esta relación es clave tanto para asegurar la precisión dimensional general y de los espesores de las paredes, como de la constitución homogénea de una capa por la correcta adyacencia de las líneas depositadas. Mientras que las variables geométricas y cinemáticas del proceso son fijadas por parámetros al momento de la programación de la operación y por lo tanto pueden ser ejecutadas con precisión, el caudal de extrusión varía dependiendo de las propiedades reológicas del material y su comportamiento en el dispositivo de extrusión.
Para construir un volumen por Material Extrusion usando cordones de material depositado, se emplea una estrategia consistente en descomponer la geometría en:
– Capas horizontales: depositando una línea de filamento adyacente a otra, en forma de zigzag o concéntrica, se va componiendo una superficie, cuya altura total será un múltiplo de la altura de la capa.
– Paredes verticales: depositando líneas de filamento adyacentes en forma continua recorriendo los perímetros externos o internos se compone una cáscara, cuyo espesor será un múltiplo del ancho del filamento.
– Relleno interno: con diversos patrones —típicamente zig zag o honeycomb— se depositan líneas no adyacentes —salvo para piezas completamente macizas— que componen una estructura reticular de densidad programable.
2.2 Aspectos críticos del proceso constructivo por extrusión y deposición
La uniformidad de la pieza está determinada por la correcta adherencia del nuevo material contra el anterior. La adherencia entre pasadas se produce por la deformación del material extruido al ser presionado sobre el previamente depositado. Para ello debe cumplirse que la relación de velocidades de extrusión y de avance sea tal que la sección depositada sea mayor que la del orificio de salida y que la altura de capa sea menor a la del orificio de salida.
Además de los movimientos de avance de la deposición para construir un cordón de material, son necesarios otros movimientos auxiliares de posicionamiento entre el fin de un cordón y el inicio de otro, durante los cuales debe pausarse la extrusión. Para lograr controlar eficazmente este ciclo se emplea la retracción, movimiento del material en sentido inverso que elimina la presión remanente en la boquilla, resultante de la elasticidad del material y del dispositivo.
Las propiedades del material, la altura de capa y el ancho depositado determinan el ángulo mínimo de las paredes verticales con respecto al plano horizontal en que se puede construir una pieza autosustentable. En esa condición, el cordón nuevo todavía puede ser soportado por el inferior; por debajo de ese mínimo es necesario la construcción de una estructura auxiliar llamada soporte, que debe ser retirada posteriormente.
2.3 Pastas cerámicas para PDM
Las pastas cerámicas consisten en sistemas heterogéneos con sólidos, agua y/o aditivos. Presentan un comportamiento plástico que permite la extrusión o cualquier otra estrategia de conformación basada en la deformación plástica, como equipos semiautomáticos de rodillos, laminadoras o tornos alfareros. Los sólidos generalmente consisten en arcillas y antiplásticos. Los aditivos pueden ser plastificantes poliméricos y/o electrolitos inorgánicos. Se pueden añadir o no aditivos plastificantes; generalmente la reología de las pastas se ajusta optimizando las operaciones de molienda (reduciendo el tamaño de grano) y/o seleccionando componentes arcillosos con mayor o menor plasticidad (Carty & Senapati, 1998).
Las pastas de arcilla se componen generalmente de materias primas naturales, tradicionalmente arcilla, cuarzo y feldespato, que se pueden representar mediante el conocido diagrama triaxial. Los sólidos generalmente se incorporan y mezclan en un molino de bolas o en un mezclador vertical.
Para la conformación de plásticos, la mezcla se realiza generalmente por vía húmeda, y luego el contenido de agua se ajusta en filtros prensa, o cualquier otra operación de secado moderada. En general, el contenido de agua y la reología adecuada para el conformado en estado plástico se logra ajustando este contenido de agua (Carter & Norton, 2013)].
Sin duda, la reología de las pastas a base de arcilla debe tenerse en cuenta para el diseño y uso de este tipo de tecnologías de fabricación. Las características reológicas de un fluido son uno de los criterios esenciales en el desarrollo de productos en un entorno industrial. Con frecuencia, estas características determinan las propiedades funcionales de los materiales e intervienen durante el control de calidad, el diseño de operaciones básicas como bombeo, mezclado y envasado, almacenamiento y estabilidad física, y más aún en la extrusión. Las propiedades reológicas se definen en función de la relación que existe entre una fuerza o sistema de fuerzas externas y su respuesta, ya sea como deformación o como flujo.
La plasticidad en el procesamiento de materiales a base de arcilla es una propiedad fundamental ya que define los parámetros técnicos para convertir una masa cerámica en una forma determinada mediante la aplicación de presión (Andrade et al., 2011). La plasticidad, en este caso, y en particular en los sistemas minerales arcillosos, se define como «la propiedad de un material que permite que se deforme repetidamente sin romperse cuando se ejerce sobre él una fuerza suficiente para provocar la deformación y que le permite conservar su forma después de la fuerza aplicada ha sido eliminada». Un sistema arcilla-agua de alta plasticidad requiere menos fuerza para deformarlo y se deforma en mayor medida sin agrietarse que uno de baja plasticidad que se deforma más fácilmente y se rompe antes (Brownell, 1976).
La plasticidad de las arcillas está relacionada con la morfología de las partículas minerales de arcilla en forma de placa que se deslizan sobre las demás cuando se agrega agua, que actúa como lubricante. A medida que aumenta el contenido de agua de la arcilla, la plasticidad aumenta hasta un máximo, dependiendo de la naturaleza de la arcilla.
3. CLASIFICACIÓN Y CRONOLOGÍA DE LA PDM DE CERÁMICOS
Para abordar el estado del arte de la I3D de materiales cerámicos por extrusión de pasta se propone un cruce entre un eje cronológico y otro tipológico, con los que analizar los casos seleccionados y encontrar la línea de evolución del conocimiento producido en el desarrollo de esta tecnología.
3.1 Cronología
Para la clasificación se abordó el conjunto de los antecedentes y se seleccionaron aquellos más representativos entre las experiencias que han logrado mejores resultados. Entre los casos analizados se distinguen cuatro grupos en el tiempo:
– Entre 2005 y 2009, los primeros extrusores experimentales desarrollados junto a las originarias impresoras de diseño abierto y bajo costo de los proyectos RepRap y Fab@Home, controladas gracias a la electrónica de fuente y código abierto del proyecto Arduino.
– Desde 2009, los extrusores de los pioneros agrupados en la comunidad de Google+ Make Your Own Ceramic 3D Printer -recientemente mudada al foro Ceramic 3D printing alojado en WikiFactory (Ceramic 3D Printing, s. f.). Iniciativas que tienen un fin experimental y exploratorio, orientadas a la producción artística y de objetos de diseño.
– Desde 2014, las primeras iniciativas comerciales de nuevas empresas proveedoras de equipos de calidad industrial, funcionamiento más amigable y de bajo mantenimiento: Lutum, Viscotec, 3DPotter, Wasp, Zmorph, Gaia.
– Desde 2017, una segunda tanda de nuevas empresas que lanzaron sus productos con propuestas de mejora de la experiencia del usuario para ampliar el mercado a un sector no especializado, en el sitio de crowfunding Kickstarter: ClayXYZ, StoneFlower, CeramBot.
3.2 Clasificación
Siguiendo con el criterio propuesto por la norma ISO, para analizar y clasificar el universo de la MA por extrusión de cerámicos en pasta (Fig. 5), nos centraremos en la metodología o partido tecnológico, concretamente en cómo son los diferentes dispositivos extrusores, en cuáles principios de funcionamiento se basan y qué resoluciones tecnológicas usan.
Todos los procesos analizados son del tipo discontinuo o batch, es decir que el volumen de pasta disponible para una operación es fija y determinada por las dimensiones de un contenedor. Ya que el modo de ampliar la capacidad del sistema es aumentar el tamaño del contenedor y por lo tanto su masa, para evitar aumentar la potencia de la máquina, la mayor parte de los casos optan por separar el contenedor de las partes móviles. Lo que lleva a una primera distinción entre los dispositivos que realizan la extrusión en una única etapa y los que suman una primera etapa de alimentación del material a una segunda de extrusión.
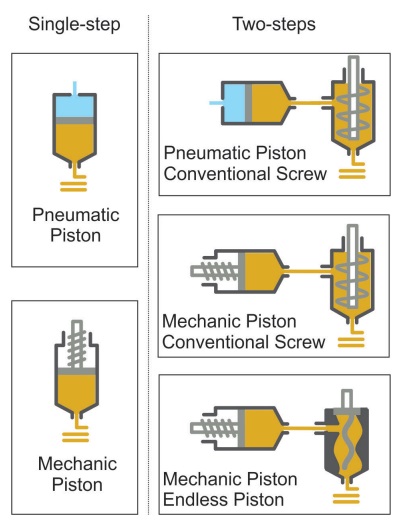
Los dispositivos de una etapa consisten en un cilindro o camisa donde se carga previamente la pasta y en un pistón o émbolo que la fuerza a fluir por una boquilla. El pistón puede ser accionado de dos modos:
– Neumático, con aire comprimido como los actuadores lineales de simple efecto.
– Mecánico, o RAM Extruder, por el empuje lineal de un mecanismo de tornillo y tuerca motorizado.
Los dispositivos de dos etapas resuelven con el pistón neumático o con el mecánico la alimentación del material a través de una manguera a la segunda etapa donde se produce la extrusión. Esta última etapa puede resolverse mediante un mecanismo motorizado de dos tipos:
– Tornillo convencional o de Arquímedes, en camisa cilíndrica, como el de las extrusoras de la industria cerámica (Handle, 2007).
– Tornillo sin fin o endless piston (Swanson, 2012), o Moineau Pump (Gravesen, 2008), como el de las bombas de cavidad progresiva, consistentes en un rotor metálico helicoidal simple y estator elastómerico con una cavidad de doble hélice.
3.3 Evolución
En la línea de tiempo ordenada según la clase de extrusor se puede observar una búsqueda orientada al control del caudal como la clave para la mejora de las morfologías posibles de obtener y así ampliar las potenciales aplicaciones de la tecnología.
La pasta cerámica arcillosa, a diferencia de los polímeros, se comporta como un material con una reología compleja, no newtoniana, en algunos casos afectada no solo por el esfuerzo de corte, sino que también dependiendo del tiempo (Bergaya & Lagaly, 2013) (Bergaya & Lagaly, 2006). Este amplio rango del comportamiento reológico de la pasta cerámica llevó la exploración hacia la búsqueda de mecanismos crecientemente «volumétricos», en el sentido del principio de las bombas de desplazamiento positivo, un dispositivo de extrusión capaz de entregar una unidad de caudal para determinada unidad de aumento de la presión o de rotación del elemento de bombeo.
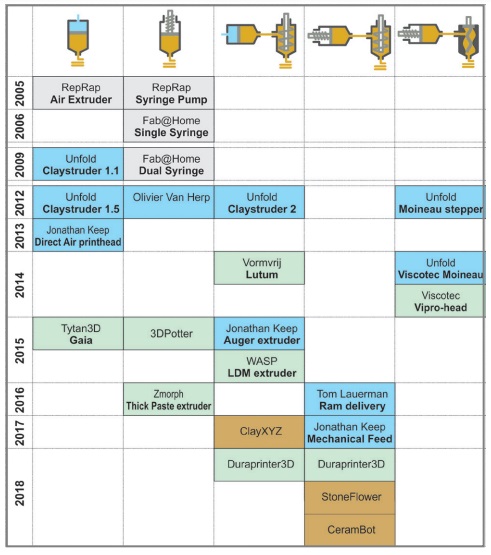
La figura 6 representa en forma esquemática la distribución de los casos estudiados según su tipología y en una línea de tiempo. A continuación, se detalla y analizan cada caso y se describen las principales características junto con las ventajas y desventajas de cada tipo de dispositivo.
3.3.1 Pistón neumático de una tapa
3.3.1.a Air Extruder
Primer extrusor neumático desarrollado en 2005 por Adrian Bowyer en los inicios del proyecto RepRap (Hodgson, 2012) en la Universidad de Bath del Reino Unido, experimentando con elementos simples como un globo, una botella plástica y una válvula solenoide controlada desde las primeras placas electrónicas de control de I3D (Fig. 7a). Aún antes del desarrollo de los extrusores calefaccionados para extrusión de filamento de polímeros —centrales en la eclosión del actual fenómeno de la I3D—, este proyecto insignia del hardware libre y del movimiento maker probaba la extrusión de pasta a temperatura ambiente en sus primeros prototipos de impresoras 3D cartesianas de escritorio de bajo costo y diseño libre, los históricos modelos Darwin y Mendel.
3.3.1.b. Claystruder 1.1 y Claystruder 1.5
Entre los pioneros de I3D de cerámica, el estudio belga UNFOLD es el que ha recorrido de la manera más sistemática la «ruta hacia el mejor extrusor de pasta» (Verbruggen, 2014). Mientras decaía el interés de los extrusores de pasta, en el movimiento maker se volcaron a desarrollar dispositivos para las impresoras de escritorio de bajo costo. En 2009 realizan una primera versión de extrusor neumático (Fig. 7b) (Unfold, 2009). El Claystruder 1.1 (Unfold, s. f.-a) consiste una jeringa de 60cc montada sobre una impresora cartesiana de escritorio mediante partes plásticas impresas en 3D, conectada a una línea de aire comprimido de hasta 8 bar, como la que se obtiene con un compresor pequeño de taller.
La primera versión contaba con una válvula solenoide para controlar en modo on-off la extrusión enlazada a la misma electrónica de la máquina. La segunda, el Claystruder 1.5 (Fig. 7c) (Unfold, s. f.-b) no tuvo válvula sino un regulador de presión de alta precisión de control manual y por lo tanto no sincronizado a los movimientos de la impresora (Unfold, 2012b).
3.3.1.c. Direct air printhead
El ceramista inglés Jonathan Keep publicó en 2013 Self Build 3D Printer, el diseño de una impresora delta para fabricación personal que tuvo gran repercusión por su solidez y sencillez constructiva y la claridad de la documentación de acceso abierto. El primer dispositivo empleado con esta máquina fue uno de aire comprimido directo. En lugar de una jeringa se aprovecha el sistema de cartuchos estándar de 310cc de las pistolas dosificadoras de adhesivos (Fig. 7d). Conectado a compresor pequeño de hasta 8 bar usa su regulador de presión y una válvula de cierre manual (Keep, 2015).
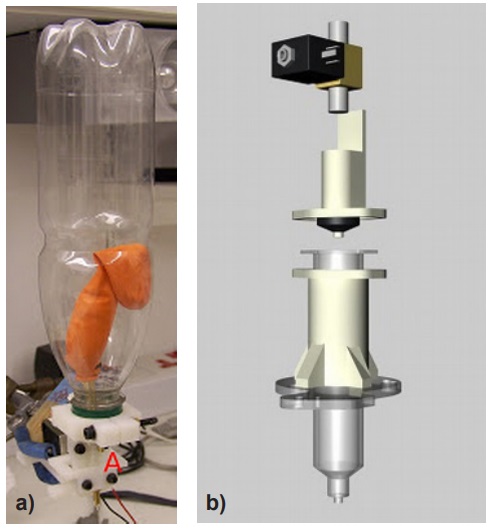
3.3.1.e. Observaciones
– Los mecanismos de Pistón Neumático son de construcción sencilla, de fácil limpieza y manipulación y pueden escalarse e independizarse de la impresora para tener mayor capacidad, conduciendo la pasta por una manguera.
– Precisan una fuente de aire comprimido externo, lo que puede ser resuelto con compresores comerciales pequeños y accesibles ya que no requieren caudal de aire, siendo más importante una presión constante.
– El control on-off del circuito de aire comprimido puede ser una válvula manual o una accionada por un solenoide en forma automática desde la electrónica de la impresora.
– El control de presión del aire es un regulador de membrana del tipo industrial —que puede ser el del mismo compresor—, aunque es preferible uno de mayor precisión.
– Su desventaja principal es la baja precisión del control de flujo de extrusión —y por lo tanto de repetibilidad del ciclo de impresión—, debida a las variaciones en la viscosidad de la pasta y en las condiciones de extrusión.
– Tampoco es posible realizar la retracción aunque pueden sí tener un mecanismo on-off de control de la extrusión.
– Permiten imprimir piezas en una sola pasada con una tolerancia amplia en el espesor de pared y resulta difícil la construcción de los fondos en forma homogénea.
– La viscosidad de la pasta debe permanecer en un rango tal que: pueda fluir por la camisa y la boquilla con presiones de aire seguras (hasta 8 bar); y que la pieza resultante del apilamiento de capas pueda sostenerse bajo su propio peso y soportar las aceleraciones de la plataforma.
3.3.1 Pistón mecánico de una tapa
3.3.2.a. Syringe Pump
También de los inicios del proyecto RepRap es la Syringe Pump de 2005 (Fig. 8a) (Hodgson, 2012). Una jeringa estándar se monta sobre un dispositivo resuelto por I3D, el émbolo es empujado por un mecanismo de tornillo tuerca motorizado.
Con el mismo esquema constructivo el proyecto Fab@Home de la Universidad de Cornwell de EEUU en 2006 produce el modelo 1 de su extrusor y en 2009 el modelo 2 (Fig 8b). El proyecto finaliza en 2012 cuando las impresoras de fabricación personal se terminan de popularizar superando en ventas a las industriales. Muchos de sus principios de diseño se pueden encontrar en modelos posteriores y durante esos años los extrusores fueron los únicos disponibles para experimentar con doble extrusión y en áreas como la bioimpresión o impresión de alimentos (Malone & Lipson, 2007) (Lipton et al., 2009).
3.3.2.b. Olivier Van Herp
En 2014 el diseñador industrial holandés Olivier Van Herpt construye su primera impresora 3D e inicia un trabajo de investigación que lo ha convertido en uno de los principales referentes mundiales por la calidad y originalidad de sus piezas cerámicas impresas (Van Herpt, 2019). Utiliza una impresora delta de grandes dimensiones y un dispositivo de pistón mecánico de gran capacidad que le permite producir piezas de hasta 1000 mm de altura y de 400mm de diámetro (Fig 8c).
3.3.2.c. 3DPotter
La empresa 3DPotter radicada en Florida, EEUU ofrece desde 2015 una familia de impresoras de alta calidad y de gran tamaño (3D Potter, s. f.). Con el objetivo de usar «verdadera arcilla» en el proceso, construyeron un pistón mecánico de gran potencia que puede empujar la pasta en unos cartuchos de 1000 a 4000 cm3 de capacidad. Para resolver el problema del elevado peso del dispositivo optaron por integrarlo al eje vertical Z de una impresora cartesiana —de movimientos relativamente lentos— mientras que la plataforma sea la que se desplaza en los ejes horizontales X e Y. Con boquillas de 3,5 a 6,4 mm de diámetro permite fabricar piezas de alfarería de hasta 508 x 432 x 762 mm de altura (Fig. 8d).
3.3.2.d. Thick Paste Extruder
De 2016 son las primeras noticias del Thick Paste Extruder (Fig. 8e) (ZMorph, 2018) de la empresa ZMorph radicada en la ciudad de Wroclaw, Polonia. Su máquina Zmorph Multitool 3D se anuncia como una de las más completas y avanzadas en equipos de escritorio de calidad industrial y funcionamiento amigable. Una serie de cabezales intercambiables posibilitan el uso en corte láser, mecanizado CNC, FDM de polímeros. El extrusor de pasta cerámica —y otros materiales como chocolate, por ejemplo— tiene una capacidad de 100ml y el volumen de trabajo es de 250 x 235 x 165 mm.
3.3.2.e. PastaBot
También en 2016 la empresa argentina Chimak 3D (Chimak3D, s. f.) presentó su dispositivo de extrusión de pasta cerámica en una etapa por pistón mecánico Pastabot. La actual versión 2 (Fig. 8f) consiste en un accesorio que se puede agregar a cualquier impresora 3D, con boquillas de 1 a 4 mm de diámetro y un sistema de cartuchos recargables.
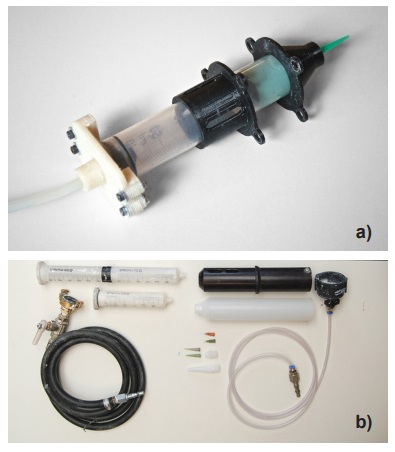
a Syringe pump; b Impresora Fab@Home con jeringa doble; c Equipo de impresión 3D de Olivier Van Herpt; d Impresora Micro9 3D Potter; e Zmorph Thick Paste Extruder; f PastaBot2
3.3.2.e. Observaciones
– El sistema de Pistón Mecánico cumple con la condición de ser «volumétrico» pero limitado al fenómeno de la elasticidad del mismo dispositivo y de la pasta
– La propia compresibilidad de las arcillas, la posible incorporación de aire en la pasta, y la deformación del cartucho por la presión interna, producen una demora entre la acción del motor y la reacción de la extrusión en la boquilla.
– Esa demora en el control de la extrusión debe ser resuelta en la configuración de los programas. La viscosidad de la pasta debe ser tal que mantenga una resistencia que no esfuerce al motor más allá de su rango seguro. En la práctica para pastas comerciales es preciso equipos de alto torque con cajas reductoras y electrónica de potencia.
– En los casos de Zmorph y de 3Dpotter el control de la extrusión está sincronizado -con un lazo de control abierto- con la electrónica de la impresora por lo que -compensando la elasticidad por programa- sería posible obtener piezas de paredes de múltiples pasadas y fondos homogéneos.
– En el caso de Olivier Van Herpt, el dispositivo de alta potencia no está sincronizado a la impresora, por lo que se limita a piezas de una pasada, no obstante lo cual, logra piezas de notable calidad con las que encabeza la vanguardia en la creación de un nuevo repertorio morfológico para esta nueva tecnología.
3.3.3. Alimentación neumática + Tronillo convencional
3.3.3.a. Claystruder2
Una segunda fase en el desarrollo del estudio UNFOLD los llevó a construir en el año 2012 el Claystruder2, un dispositivo de dos etapas: una jeringa de 60cc conectada a una línea de aire comprimido actuaba como cartucho de alimentación de la pasta a una segunda etapa en el que un tornillo sinfín -motorizado por un motor paso a paso sincronizado con la impresora- la fuerza a fluir por la boquilla. (Unfold, 2012c).
3.3.3.b. LDM extruder
El colectivo World`s Advanced Saving Project (WASP) se forma en Rávena, Italia con el objetivo de la difusión social de la innovación tecnológica. Entre sus antecedentes se encuentra el de la construcción de una impresora delta de escala arquitectónica para imprimir partes de casas mediante la extrusión de adobe (Wasp, s. f.-a).
En octubre de 2014 prueban una exitosa primera versión de un dispositivo a tornillo con alimentación neumática. El conocimiento obtenido los consolidó como un referente de impresoras 3D de uso industrial de grandes dimensiones del tipo FDM y especializadas en cerámica en particular. El kit de extrusión (Fig. 9d) en el año 2015 presentaba notables mejoras con respecto a los modelos anteriores de fabricación casera. La primera etapa constaba de un tanque metálico de 3l con dos tapas que facilitan la carga y la limpieza, conectado la línea de aire mediante un regulador de presión que alimenta mediante una manguera al extrusor de tornillo LDM por Liquid deposit modeling (Wasp, s. f.-b). El extrusor LDM está diseñado para un sencillo armado y fácil limpieza y puede ser montado en cualquier impresora. En la actualidad WASP ofrece sus impresoras delta en dos tamaños Ø200 mm x H400 mm y Ø400 mm x H1000 mm y su software de control cuenta con facilidades y mejoras específicas para I3D de pasta cerámica.
3.3.3.c. Lutum auger system
Desde 2014 la empresa holandesa VormVrij (VormVrij, s. f.) ofrece su línea Lutum de impresoras (Fig. 9c), cartuchos y extrusores, que se encuentran entre los diseños más avanzados del mercado. La impresora es del tipo cartesiana, la base forma una amplia plataforma fija y el cabezal es el que se mueve en los tres ejes con una configuración en voladizo que deja libre de obstáculos el volumen de trabajo —430 x 460 mm en XY y 500 u 800 mm en Z—. El extrusor está resuelto en metales revestidos para una mayor durabilidad y para un excelente sellado y facilidad de montaje y limpieza (Van Den Heerk, 2017). Soporta directamente cartuchos de 650 y 1400 cc; pueden usarse cartuchos de mayor capacidad, pero externos a la impresora y conectados por manguera. Ofrece una versión de doble extrusor para impresiones a dos materiales. La base de la máquina tiene integrado el sistema de regulación de presión de aire.
3.3.3.d. Auger extruder printhead
También Jonathan Keep incorporó a su impresora delta un dispositivo de dos etapas de fabricación casera (Fig. 9b) con el mismo principio de funcionamiento, pero de mayor capacidad que el de UNFOLD. A pesar de la relativa precariedad constructiva, con este equipamiento produjo una obra con gran reconocimiento por su calidad técnica y su innovador enfoque, como la serie de vasijas generadas a partir de sonidos (Keep, 2015).
3.3.3.e. ClayXYZ
De la nueva generación de empresas iniciadas en la plataforma de financiamiento colaborativo Kickstarter dedicadas a la I3D de cerámica es ClayXYZ la que ofrece un sistema de extrusión a tornillo con una alimentación neumática mediante un compresor de aire especializado que promete un flujo continuo y eliminación de burbujas de la pasta. El diseño del emprendimiento iniciado en 2017 radicado en Nueva York cuenta con numerosos avances en la simplificación de la operación para acercar la tecnología a usuarios no especializados (ClayXYZ, s. f.).
3.3.3.f. Duraprinter
Desde 2018 el Grupo DuraCer, de Río de Janeiro, Brasil, ofrece sus productos a centros de investigación y desarrollo, así como a artistas y artesanos, bajo la marca comercial de «DuraPrinter» (DuraCer Group, s. f.). Tienen tres tamaños de impresoras deltas, con volúmenes de trabajo de 145 a 300 mm en diámetro y 180 a 600 mm en altura. El extrusor a tornillo convencional está provisto con boquillas de 2 a 10 mm y también puede ser montado con jeringas estándar. La pasta se transporta al extrusor desde un contenedor con capacidades de entre 0,3 a 5,0 litros, presurizada por compresores o por gas de un cilindro presurizado (Fig. 9e). El grupo DuraCer también provee sistemas de alimentación electromecánicos, con capacidad de 1,1 litros y puede operar desde los 0,1 litros.
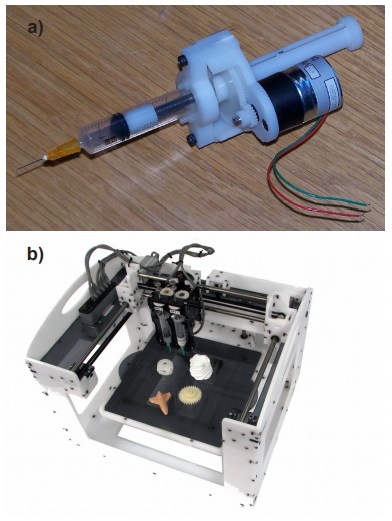
a Claystruder2; b Impresora Delta con Auger extruder printhead; c Impresora 3D Lutum: d Kit de extrusión Wasp; e Impresoras DuraPrinter y detalle del contenedor de 2,5l.
3.3.3.g. Observaciones
– El sistema de alimentación neumática y extrusión a tornillo no es estrictamente «volumétrico»: siendo el canal del tornillo sinfín un continuo, la presión del alimentador se propaga hasta la boquilla. Por lo tanto, para una misma velocidad de giro del tornillo, el caudal varía con la presión de la primera etapa. Según Dixon (Dixon, 1996) «viscosity metering pumps» es una mejor definición para este dispositivo.
– No obstante, en condiciones constantes de viscosidad de la pasta es posible lograr un buen control del flujo en la boquilla. Gracias a la posibilidad de retracción —mediante el cambio de giro del tornillo— se logra parar rápidamente la extrusión para luego retomarla después de un movimiento auxiliar.
– En condiciones estables es posible imprimir piezas de paredes múltiples y rellenos homogéneos de las caras horizontales de los fondos.
– Con cada nueva carga —y según su viscosidad— la presión de aire debe ser regulada en pruebas de calibración de acuerdo al espesor de pasada programado.
3.3.4. Alimentación mecánica + Tornillo convencional
3.3.4.a. RAM Delivery + Auger Extruder
Recientemente Tom Lauerman publica sus avances en la construcción de un sistema de extrusor a tornillo alimentado por un pistón mecánico (Fig. 10a) (Lauerman, 2019). Luego de unos años de desarrollar equipos y explorar las posibilidades morfológicas del proceso, este investigador de la Penn State University’s School of Visual Arts en Nueva York, EEUU, y uno de los principales animadores de la comunidad Ceramic 3D Printing, logra en 2016 importantes avances en la sincronización de ambas etapas aprovechando la capacidad de las placas Arduino y Ramps de controlar más de un extrusor simultáneamente, previamente desarrollado para la impresión de plásticos multicolor mediante la mezcla de filamentos en extrusores múltiples.
3.3.4.b. Mechanical clay feed
En 2017 Jonathan Keep publica una versión de alimentador mecánico (Fig. 10b) que reemplaza el neumático y trabaja en conjunto con el anterior extrusor a tornillo. El alimentador resultó ser de gran porte en relación a la capacidad de carga del cartucho y la elasticidad de los materiales empleados resultaron en una complicación en la sincronización de ambos motores (Keep, 2017).
3.3.4.c. StoneFlower
Con un lanzamiento en Kickstarter en 2018 se incorpora al mercado StoneFlower -un emprendimiento radicado en Munich, Alemania- con su kit de extrusión de cerámica adaptable a cualquier impresora 3D de escritorio (Fig. 10c). El diseño del extrusor a tornillo proviene de los antecedentes de la comunidad maker y es ofrecido con una licencia abierta. El principal aporte es la resolución de un sólido y práctico pistón mecánico para la alimentación. El cartucho de plástico transparente tiene una capacidad de 500 cm3, un motor de alto torque permite extruir pastas de baja viscosidad y un sistema integrado de control que aseguran permite alta precisión del proceso (StoneFlower, s. f.).
3.3.4.d. Cerambot
También en 2018 inicia en Kickstarter su propuesta de un kit de extrusión adaptable a impresoras de escritorio la empresa Cerambot de la ciudad de Jinan, China. Ofrecen en forma conjunta o independiente su impresora delta y dos kits alternativos, un extrusor a tornillo alimentado en forma neumática o mecánica (Fig. 10d). Como principal rasgo de mejora manifiesta haber logrado un sistema más veloz y preciso que los antecedentes (Cerambot, s. f.).
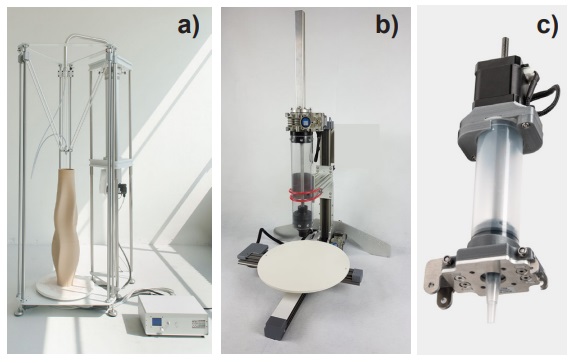
a Impresora con RAM Delivery + Auger Extruder; b Impresora delta con Mechanical clay feed; c Alimentador y extrusor Stoneflower; d Impresora, kit neumático y kit mecánico de Cerambot
3.3.4.e. Observaciones
– A diferencia de la clase anterior de alimentación neumática, la alimentación mecánica por el mecanismo de tornillo/tuerca motorizada puede ser sincronizada en forma electrónica y resolver los problemas de la elasticidad del sistema.
– El control de la extrusión y la retracción hace posible imprimir piezas de paredes múltiples y rellenos homogéneos de las caras horizontales de los fondos.
-No precisa una fuente de aire comprimido externa.
– A igual tamaño del cartucho que la alimentación neumática permite lograr mayores fuerzas de empuje del pistón y por lo tanto trabajar con pastas más densas que logren piezas como mayor resistencia para soportar su propio peso y los esfuerzos durante la deposición.
– El dispositivo de alimentación es voluminoso y pesado, y el motoreductor de alto torque requiere una electrónica de potencia.
3.3.5. Alimentación neumática + Tronillo sin fin
3.3.5.a. Moineau stepper extruder
En su búsqueda de un dispositivo completamente volumétrico Dries Verbruggen y Claire Wainer de UNFOLD dirigen su investigación al principio de las bombas de cavidad progresiva. Su primera aproximación de 2012 (Fig. 11a) fue un dispositivo impreso en plástico a partir de un diseño de acceso abierto, alimentado con una jeringa estándar de 60 cm3 impulsada por aire comprimido. Con esta experiencia pudo validar el principio de funcionamiento, pero también se encontró con las limitaciones de la FDM en cuanto a la resistencia de las piezas y ajuste dimensional del conjunto (Unfold, 2012a).
3.3.5.b. Unfold Viscotec Moineau Pump
En 2014 Unfold en asociación con la empresa alemana Viscotec, líder global en soluciones de dosificación, pone a prueba un extrusor de tornillo sin fin de calidad industrial adaptado a cerámica con una alimentación neumática, logrando excelentes resultados en cuanto al control de extrusión a diferentes velocidades (Fig. 11b) (Unfold, 2014).
3.3.5.c. Vipro-head
En 2014 la empresa ViscoTec lanza al mercado un extrusor de tornillo sin fin específico para I3D. El Vipro-head (Fig. c) es un sofisticado, compacto y preciso extrusor de pastas y materiales viscosos, que puede ser acoplado a impresoras 3d de escritorio (Viscotec, s. f.). Permite extruir en muy pequeños diámetros para lograr piezas de muy buen detalle. Cuenta con control de temperatura y una versión de doble alimentación para mezcla de materiales de dos componentes. Su alto costo y limitación en tamaño lo hace aplicable más en bioimpresión e investigación de materiales que en la producción de piezas de cerámica tradicional.
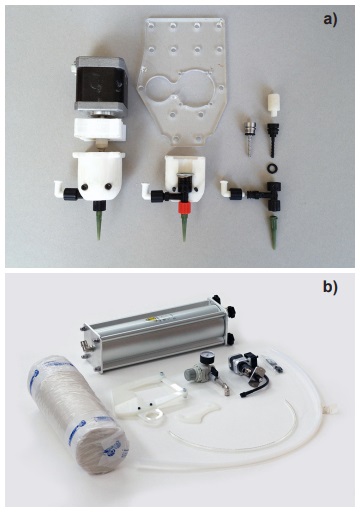
3.3.5.d. Observaciones
– Las bombas de cavidad progresiva son completamente volumétricas por lo tanto la extrusión es independiente de la viscosidad del material.
– La transmisión entre motor y tornillo sin fin debe ser el de una doble unión cardánica; bastante más compleja que las transmisiones directas simples de otros mecanismos.
– El rotor metálico helicoidal y el estator elástico de doble hélice son piezas formalmente complejas y de gran precisión dimensional por lo tanto de construcción compleja que requiere tecnologías de producción altamente especializadas como el mecanizado CNC con cuarto eje.
– Los antecedentes existentes deben montarse sobre las partes móviles de la impresora lo cual limita el peso del dispositivo y la capacidad de carga, por lo que resulta una técnica adecuada para materiales de alto valor agregado y piezas pequeñas que requieren buena resolución dimensional.
4. PROYECTO UNLa-CETMIC DE I3D CERÁMICA
Desde el año 2012, la Licenciatura en Diseño Industrial de la Universidad Nacional de Lanús (UNLa) y el Centro de Tecnología en Recursos Minerales y Cerámica (CETMIC, CIC-CONICET) trabajan de manera multidisciplinar en esta área. La investigación y el desarrollo han abarcado a un conjunto de aspectos: la determinación y preparación del material; los dispositivos de extrusión; los parámetros de programación; la I3D en sí; los pasos posteriores al conformado —secado, cocción, esmaltado—; las posibilidades morfológicas y las condicionantes tecnológicas para el diseño de objetos.
En el transcurso del trabajo se diseñaron y se llevaron a fase prototipo de laboratorio diversos dispositivos de I3D de pastas. Por un lado, se construyó un dispositivo de dos etapas —alimentación neumática y extrusor de tornillo convencional— con capacidad de 3kg de pasta y tamaño de piezas de hasta 200 x 200 x 200 mm; diseño que tuvo diversas etapas ( Fig. 12 a,b,c) (Ruscitti et al., 2017a) (Ruscitti et al., 2017b) (Ruscitti et al., 2017c). Por otro, se incorporó al laboratorio un dispositivo de pistón mecánico directo que aprovecha un sistema de jeringa comercial de 60cc, para actividades de ensayo y caracterización de materiales (Fig. 12d) (Ruscitti et al., 2018).

a, b, c, Dispositivos de alimentación neumática y de tornillo convencional, versiones 1, 2 y 3; d Dispositivo de una etapa por pistón mecánico
Con miras a la aplicación en el campo de la ingeniería de materiales, diseño de producto, arquitectura, artesanía y arte, se continúan explorando los aspectos tecnológicos a medida que se llevan a cabo actividades de difusión y de transferencia de la innovación al medio productivo y la comunidad.
5. COMENTARIOS FINALES
En relación a otras técnicas de MA de cerámica la PDM presenta por un lado deficiencias en cuanto a precisión dimensional, a complejidad morfológica y al aprovechamiento de materiales avanzados y por otro lado importantes ventajas en cuanto al tamaño de las piezas, menores tiempos de conformado, más bajos costos y mejor disponibilidad de los insumos, equipamiento más barato y de más fácil mantenimiento, un mayor grado de avance de la innovación en aplicaciones cotidianas y una importante difusión del conocimiento científico tecnológico en la sociedad y la industria. En vista de los antecedentes existentes se puede afirmar que la alfarería artesanal y la producción industrial de cerámicos tradicionales está efectivamente ingresando a su etapa digital con el desarrollo de la PDM, tal como viene sucediendo en otros campos tecnológicos. Sin embargo, para lograr consolidar las incipientes innovaciones se requiere afrontar algunos desafíos estrictamente tecnológicos y otros relacionados con el diseño de producto y la búsqueda de nuevas aplicaciones.
La formulación y preparación de las pastas debe mejorarse para lograr condiciones de proceso más estables, previsibles y repetibles. El desaireado de la materia prima —ya resuelto en los procesos industriales tradicionales— suele ser un problema frecuente. El agua es el único solvente empleado para lograr la reología adecuada, la exploración de otros componentes plastificantes podría facilitar la extrusión, mejorar la resistencia de la pieza durante la deposición y traer beneficios en el secado. La investigación en pastas basadas en materiales avanzados podría resolver parte de las dificultades de las pastas arcillosas y abrirían la tecnología a aplicaciones de alto valor agregado.
La integración de extrusores de pasta cerámica en sistemas diseñados para plásticos requiere mayores adaptaciones. El rango del comportamiento de una pasta de arcilla obtenida en forma artesanal o industrial —no exclusivamente de laboratorio— es mucho mayor que la de los filamentos de polímero disponibles para FDM. No sólo entre un lote y otro, sino durante una misma carga puede variar la plasticidad del material, lo cual es un problema para un sistema de control de lazo abierto.
Para el campo del diseño de producto se presenta el desafío de la exploración de morfologías que aprovechen los rasgos característicos del proceso para crear nuevos productos con su propia expresividad, que propongan nuevas formas a productos cotidianos y que también amplíen los usos y aplicaciones de la cerámica.
De reciente aparición en Argentina, la I3d de cerámica cuenta con algunos antecedentes que pueden constituir una plataforma para una creciente incorporación de la tecnología en el medio productivo local y para consolidar una línea de desarrollo en Manufactura Digital, uno de los sectores estratégicos para la soberanía tecnológica en tiempos de la cuarta revolución industrial.
6. AGRADECIMIENTOS
Los autores expresan su agradecimiento a la Universidad Nacional de Lanús y al Consejo Nacional de Investigaciones Científicas y Técnicas por su apoyo. Este trabajo ha sido parcialmente financiado por el Proyecto de Investigación Orientada Desarrollo de una tecnología de impresión 3D por sistema de extrusión-deposición de materiales cerámicos, PIO CONICET-UNLa 2016-2018. Nro: 22420160100023CO.
*Andrés Ruscitti, Diseñador Industrial. Laboratorio de Diseño, Departamento de Humanidades y Artes, Universidad Nacional de Lanús.
**Clara Tapia, Diseñadora Industrial. Laboratorio de Diseño, Departamento de Humanidades y Artes UNLa.
***Nicolás M. Rendtorff, Diseñador Industrial. CETMIC Centro de recursos Minerales y Cerámica (CIC-CONICET La Plata).
Nota: Versión en castellano del artículo original de los mismos autores, publicado en 12/2021, en inglés, en Revista Cerâmica Vol. 66, pps 354-366. https://doi.org/10.1590/0366-69132020663802918; Attribution-NonCommercial 4.0 International (CC BY-NC 4.0), corregida en el apartado sobre cronología gracias a los comentarios de Jonhatan Keep, con el agregado de los apartados 3.3.2e y 4.
BIBLIOGRAFÍA
3D Potter. (s. f.). 3D Potter. Recuperado 1 de abril de 2019, de https://3dpotter.com/
3DHUBS. (s. f.). Additive_Manufacturing_Infographic. Recuperado 15 de marzo de 2019, de https://drnm.me/wp-content/uploads/2018/10/additive-manufacturing-infographic-additive-manufacturing-technologies-3dprinting-3dprintinginfographic-16m.png
Andrade, F. A., Al-Qureshi, H. A., & Hotza, D. (2011). Measuring the plasticity of clays: A review. Applied Clay Science, 51(1), 1-7. https://doi.org/10.1016/j.clay.2010.10.028
Bergaya, F., & Lagaly, G. (2006). General Introduction: Clays, Clay Minerals, and Clay Science. En Developments in Clay Science (Vol. 1, pp. 1-18). Elsevier. https://doi.org/10.1016/S1572-4352(05)01001-9
Bergaya, F., & Lagaly, G. (2013). Handbook of Clay Science (Vol. 5). Newnes.
Brownell, W. E. (1976). Structural Clay Products. Springer-Verlag. https://doi.org/10.1007/978-3-7091-8449-3
Carter, C. B., & Norton, M. G. (2013). Industry and the Environment. En C. B. Carter & M. G. Norton (Eds.), Ceramic Materials: Science and Engineering (pp. 713-728). Springer New York. https://doi.org/10.1007/978-1-4614-3523-5_38
Carty, W. M., & Senapati, U. (1998). Porcelain—Raw Materials, Processing, Phase Evolution, and Mechanical Behavior. Journal of the American Ceramic Society, 81(1), 3-20. https://doi.org/10.1111/j.1151-2916.1998.tb02290.x
Cerambot. (s. f.). CERAMBOT, Digital Ceramics Studio. Recuperado 1 de abril de 2019, de https://www.cerambot.com/
Ceramic 3D Printing. (s. f.). Wikifactory. Recuperado 15 de junio de 2019, de https://wikifactory.com/+Ceramic3DPrinting
Chen, Z., Li, Z., Li, J., Liu, C., Lao, C., Fu, Y., Liu, C., Li, Y., Wang, P., & He, Y. (2019). 3D printing of ceramics: A review. Journal of the European Ceramic Society, 39(4), 661-687. https://doi.org/10.1016/j.jeurceramsoc.2018.11.013
Chimak3D. (s. f.). Chimak 3D – IMPRESORAS 3D. Recuperado 4 de agosto de 2020, de http://www.chimak3d.com/
ClayXYZ: Desktop 3D Clay Printer, Create Your Own Artwork! (s. f.). Kickstarter. Recuperado 1 de abril de 2019, de https://www.kickstarter.com/projects/clayxyz/clayxyz-desktop-3d-clay-printer-create-your-own-ar
Deckers, J., Vleugels, J., & Kruth, J.-P. (2014). Additive manufacturing of ceramics: A review. Journal of Ceramic Science and Technology, 5(4), 245-260. https://doi.org/10.4416/JCST2014-00032
Dixon, D. (1996). Archimedes Pumps. http://www3.uic.com/wcms/images2.nsf/(GraphicLib)/Archimedes_Pumps.PDF/$File/Archimedes_Pumps.PDF
DuraCer Group. (s. f.). DuraPrinter3d. DuraPrinter3d. Recuperado 9 de abril de 2020, de https://duraprinter3d.com/en/
Fressoli, J. M., & Smith, A. (2015). Impresiones 3D: Fabricación digital ¿Una nueva revolución tecnológica? http://ri.conicet.gov.ar/handle/11336/69861
Gershenfeld, N. (2012). How to Make Almost Anything, The Digital Fabrication Revolution. Foreign Affairs, 91(6), 16.
Gravesen, J. (2008). The geometry of the Moineau pump. Computer Aided Geometric Design, 25(9), 792-800. https://doi.org/10.1016/j.cagd.2008.06.012
Handle, F. (2007). Extrusion in Ceramics. Springer Science & Business Media.
Hodgson, G. (2012). A History of RepRap Development. https://reprap.org/mediawiki/images/a/a5/A_History_of_RepRap_Development.pdf
Huang, Y., Leu, M. C., Mazumder, J., & Donmez, A. (2015). Additive Manufacturing: Current State, Future Potential, Gaps and Needs, and Recommendations. Journal of Manufacturing Science and Engineering, 137(1). https://doi.org/10.1115/1.4028725
ISO/ASTM. (2015). ISO/ASTM 52900:2015. ISO. http://www.iso.org/cms/render/live/en/sites/isoorg/contents/data/standard/06/96/69669.html
Keep, J. (2015). Make your own 3D delta printer for ceramic. http://www.keep-art.co.uk/Self_build.html
Keep, J. (2017). Make your own clay auger printhead with mechanical ram delivery. http://www.keep-art.co.uk/printhead.html
Lauerman, T. (2019, enero 13). 3D Printing in Clay: Using A Synchronized Auger Extruder With a Mechanical Supply Feed. Tom Lauerman. https://tomlauerman.com/blog/2018/12/5/3d-printing-in-clay-using-a-synchronized-mechanical-feed-and-auger-extruder
Lipton, J. I., Cohen, D., Heinz, M., Lobovsky, M., Parad, W., Bernstein, G., Li, T., Quartiere, J., Washington, K., Umaru, A.-A., Masanoff, R., Granstein, J., Whitney, J., & Lipson, H. (2009). Fab@Home Model 2: Towards Ubiquitous Personal Fabrication Devices. 12.
Malone, E., & Lipson, H. (2007). Fab@Home: The personal desktop fabricator kit. Rapid Prototyping Journal, 13(4), 245-255. https://doi.org/10.1108/13552540710776197
Ruscitti, A., Rendtorff Birrer, N. M., & Serra, M. F. (2017a). Dispositivo de Impresión 3D de Pasta Cerámica UNLa-CETMIC, por alimentación neumática y extrusión a tornillo, Versión 1. Repositorio José María Rosa.
Ruscitti, A., Rendtorff Birrer, N. M., & Serra, M. F. (2017b). Dispositivo de Impresión 3D de Pasta Cerámica UNLa-CETMIC, por alimentación neumática y extrusión a tornillo, Versión 2. https://doi.org/10.18294/rdi.2019.175798
Ruscitti, A., Rendtorff Birrer, N. M., & Serra, M. F. (2017c). Dispositivo de Impresión 3D de Pasta Cerámica UNLa-CETMIC, por alimentación neumática y extrusión a tornillo, Versión 3. https://doi.org/10.18294/rdi.2019.175799
Ruscitti, A., Rendtorff Birrer, N. M., Serra, M. F., & Stabile, M. (2018). Dispositivo de Impresión 3D de Pasta Cerámica UNLa-CETMIC, por extrusión con pistón mecánico para jeringa estándard. https://doi.org/10.18294/rdi.2019.175801
Slic3r. (s. f.). Slic3r Manual – Flow Math. Recuperado 15 de marzo de 2019, de https://manual.slic3r.org/advanced/flow-math
StoneFlower. (s. f.). StoneFlower ceramic 3d printer. Recuperado 1 de abril de 2019, de https://www.stoneflower3d.com/
Swanson, P. (2012). The “Endless Piston” Pump—Technology for Precision Dispensing. 6.
Travitzky, N., Bonet, A., Dermeik, B., Fey, T., Filbert‐Demut, I., Schlier, L., Schlordt, T., & Greil, P. (2014). Additive Manufacturing of Ceramic-Based Materials. Advanced Engineering Materials, 16(6), 729-754. https://doi.org/10.1002/adem.201400097
Unfold. (s. f.-a). Claystruder 1.1. Recuperado 28 de noviembre de 2019, de https://www.thingiverse.com/thing:3604
Unfold. (s. f.-b). Claystruder 1.5. Recuperado 28 de noviembre de 2019, de https://www.thingiverse.com/thing:21788
Unfold. (2009, diciembre 28). Design for the extruder (on short hold). Unfold ~fab. http://unfoldfab.blogspot.com/2009/12/design-for-extruder-on-short-hold.html
Unfold. (2012a). Moineau stepper extruder Luer lock updates by unfold. https://www.thingiverse.com/thing:16741
Unfold. (2012b, abril 22). Road to better paste extrusion, episode 1: Recap. Unfold ~fab. http://unfoldfab.blogspot.com/2012/04/road-to-better-paste-extrusion-episode.html
Unfold. (2012c, agosto 6). Road to better paste extrusion, episode 2: Auger Valves. Unfold ~fab. http://unfoldfab.blogspot.com/2012/08/road-to-better-paste-extrusion-episode.html
Unfold, U. (2014, diciembre 26). Road to Better Paste Extrusion, episode 3: Industrial quality 3D printing of paste materials with ViscoTec Moineau Pump. Unfold ~fab. http://unfoldfab.blogspot.com/2014/12/Unfold-Viscotec-Professional-Paste-3D-Printing.html
Van Den Heerk, Y. (2017, diciembre 6). Full Length Feature: The LUTUM® Auger system. 3Dclayprinting. https://3dclayprinting.com/full-feature-advantages-and-disadvantages-of-the-lutum-auger-system/
Van Herpt, O. (2019). Explorations in functional 3D Printing Ceramics. http://oliviervanherpt.com/functional-3d-printed-ceramics/
Verbruggen, D. (2014, marzo 19). The road to better paste extrusion. Unfold ~fab. http://unfoldfab.blogspot.com/2014/03/reprap-magazine.html
Viscotec. (s. f.). Fluids & paste printing with 3D print heads based on endless piston principle. ViscoTec Pumpen- u. Dosiertechnik GmbH. Recuperado 1 de abril de 2019, de https://www.viscotec.de/en/industry-applications/3d-printing/
VormVrij. (s. f.). LUTUM site – Clay and Ceramics 3dprinters by VormVrij® 3D. Recuperado 1 de abril de 2019, de https://lutum.vormvrij.nl/
Wasp, W. (s. f.-a). BigDelta WASP 12MT Stampanti 3D. Recuperado 1 de abril de 2019, de https://www.3dwasp.com/en/giant-3d-printer-bigdelta-wasp-12mt/
Wasp, W. (s. f.-b). Clay Kit 2.0 with LDM Wasp extruder. Recuperado 1 de abril de 2019, de https://www.personalfab.it/en/shop/clay-extruder-kit-2-0/
Wohlers, T., & Gornet, T. (2016). History of additive manufacturing. Wohlers Report, 24.
ZMorph. (2018). Thick Paste Extruder. https://zmorph3d.com/